The Scientific Research Behind Porosity: A Comprehensive Guide for Welders and Fabricators
Understanding the elaborate systems behind porosity in welding is crucial for welders and makers aiming for remarkable craftsmanship. From the composition of the base products to the details of the welding procedure itself, a plethora of variables conspire to either exacerbate or ease the existence of porosity.
Understanding Porosity in Welding
FIRST SENTENCE:
Examination of porosity in welding reveals important understandings into the integrity and quality of the weld joint. Porosity, defined by the presence of cavities or gaps within the weld metal, is a typical worry in welding processes. These spaces, otherwise correctly addressed, can compromise the architectural integrity and mechanical homes of the weld, resulting in potential failures in the ended up item.
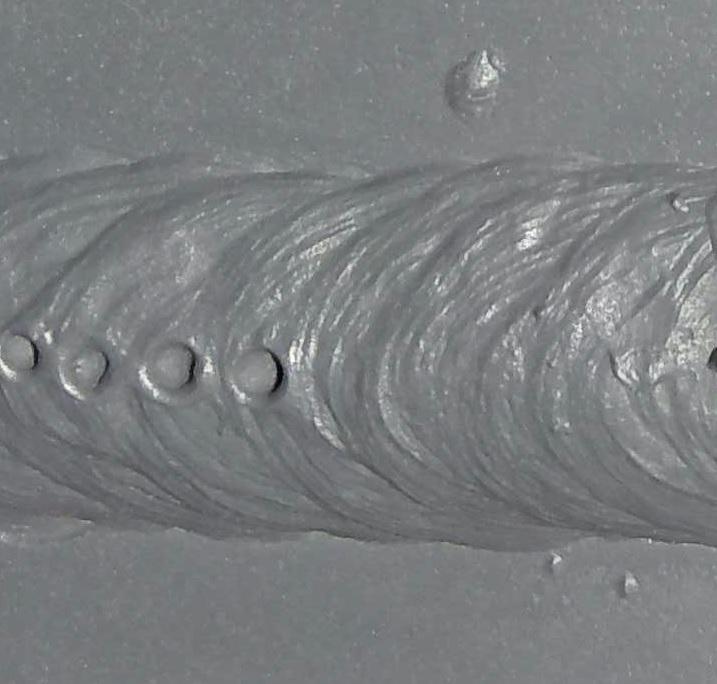
To identify and evaluate porosity, non-destructive screening techniques such as ultrasonic screening or X-ray assessment are often employed. These strategies permit for the recognition of inner defects without jeopardizing the integrity of the weld. By examining the size, form, and distribution of porosity within a weld, welders can make educated decisions to enhance their welding procedures and accomplish sounder weld joints.
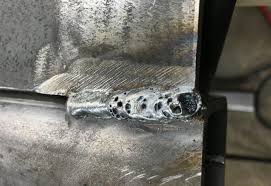
Variables Affecting Porosity Formation
The event of porosity in welding is affected by a myriad of elements, varying from gas protecting effectiveness to the ins and outs of welding specification setups. Welding parameters, consisting of voltage, current, take a trip speed, and electrode type, additionally effect porosity formation. The welding technique utilized, such as gas metal arc welding (GMAW) or secured steel arc welding (SMAW), can influence porosity formation due to variants in heat circulation and gas insurance coverage - What is Porosity.
Effects of Porosity on Weld High Quality
Porosity development significantly compromises the structural integrity and mechanical residential or commercial properties of welded joints. When porosity is existing in a weld, it produces voids or tooth cavities within the product, minimizing the total stamina of the joint. These voids work as stress and anxiety concentration factors, making the weld much more susceptible to fracturing and failure under lots. The presence of porosity likewise weakens the weld's resistance to rust, as the caught air or gases within the voids can respond with the surrounding setting, causing degradation gradually. Additionally, porosity a fantastic read can prevent the weld's capability to withstand pressure or effect, additional jeopardizing the overall top quality and dependability of the welded framework. In vital applications such as aerospace, automotive, or architectural constructions, where security and longevity are vital, the detrimental impacts of porosity on weld high quality can have extreme consequences, emphasizing the importance of reducing porosity with appropriate welding methods and treatments.
Techniques to Minimize Porosity
In addition, utilizing the appropriate welding specifications, such as the appropriate voltage, present, and take a trip rate, is essential in stopping porosity. Keeping a constant arc size and angle throughout welding basics likewise helps lower the probability of porosity.

Additionally, selecting the right shielding gas and keeping proper gas flow rates are necessary in minimizing porosity. Making use of the suitable welding method, such as back-stepping or utilizing a weaving movement, can additionally aid distribute warmth equally and reduce the opportunities of porosity formation. Finally, making sure appropriate ventilation in the welding atmosphere to remove any kind of prospective resources of contamination is essential for accomplishing porosity-free welds. By applying these methods, welders can efficiently reduce porosity and produce top quality welded joints.

Advanced Solutions for Porosity Control
Carrying out innovative innovations and innovative methods plays a crucial function in achieving premium control over porosity in welding processes. In addition, using advanced welding strategies such as pulsed MIG welding or modified ambience welding can likewise help reduce porosity problems.
An additional sophisticated solution entails making use of advanced welding devices. For circumstances, utilizing devices with integrated functions like waveform control and sophisticated power sources can enhance weld quality and lower porosity dangers. The implementation of automated welding systems with accurate control over criteria can dramatically reduce porosity defects.
Additionally, including sophisticated surveillance and evaluation technologies such as real-time X-ray imaging or automated ultrasonic screening can aid in detecting porosity early in the welding process, permitting immediate corrective actions. Generally, incorporating these advanced options can greatly boost porosity control and improve the total high quality of welded elements.
Conclusion
In verdict, recognizing the science behind porosity in welding is important for welders and fabricators to create top notch welds - What is Porosity. Advanced remedies for porosity control can additionally improve the welding process and make sure a strong and reputable click for more info weld.